A new take on supply chains
The global economy is picking up once more. But the sharp rise in demand has to navigate not only the continuing pandemic but, increasingly, also material shortages. This presents a historic challenge and a real test for supply chains and global networks. Completely abandoning globalization, however, is not an option.
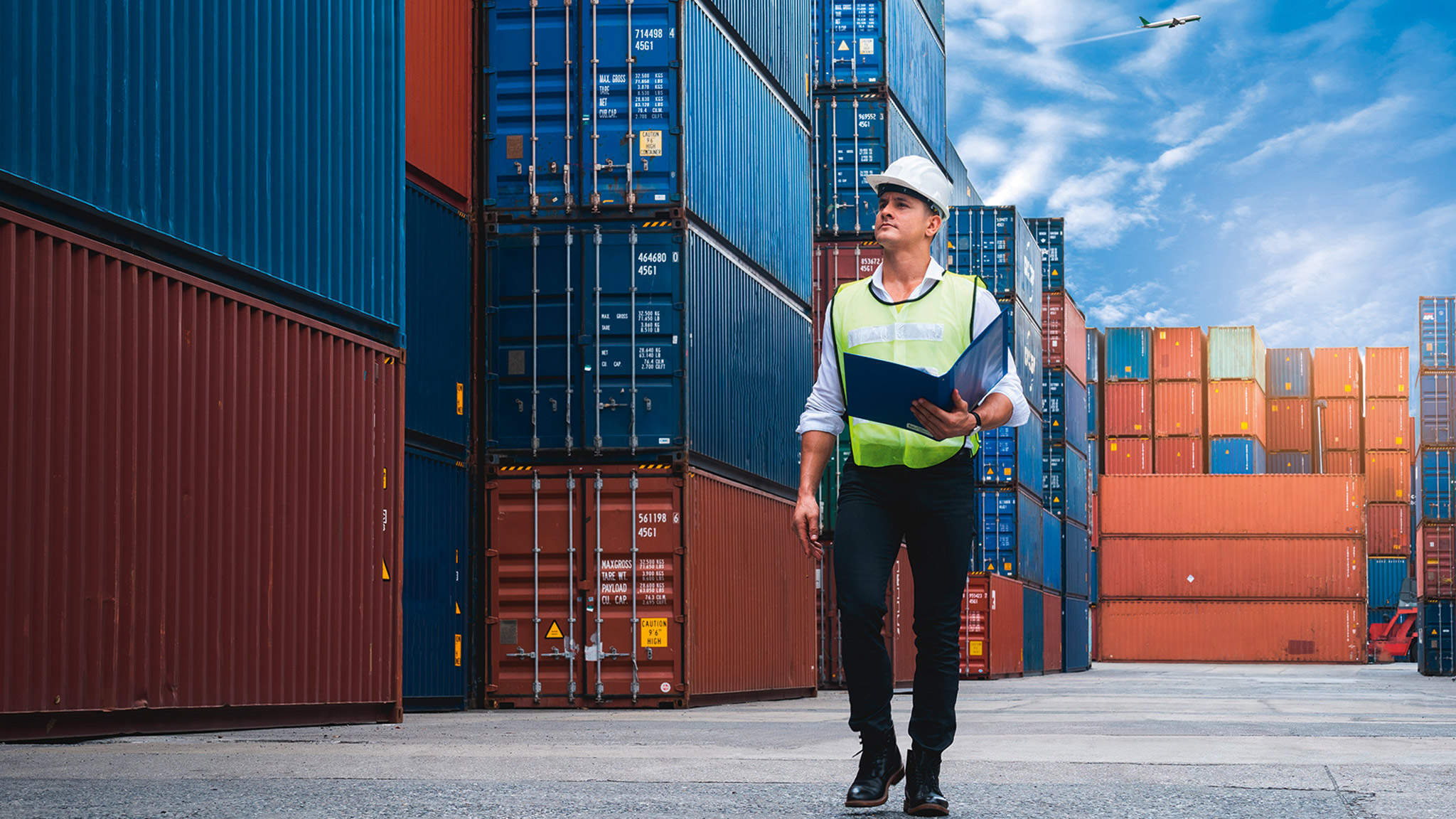
It’s a bit like brushing your teeth in the morning—you don’t have to give it much thought, the motions are obvious. The supply chains in our extensively globalized economy work in a similar way. Wherever production runs on a demand-oriented and, ideally, just-in-time basis, and whenever there’s a need to get products and intermediate products to customers, global logistics networks draw on sophisticated, fully digitalized supply chain management to provide their services. And they deploy people who are adept at getting all kinds of goods from A to B. In “normal” times, this would be smooth sailing: companies would work in line with their own control mechanisms and the customers’ expectations. As straightforward as the morning routine.
But the pandemic has unhinged many certainties. Global supply chains are encountering disruption after disruption for all sorts of reasons. Take the giant container ship Ever Given, for example, which ran aground in the Suez Canal, creating a backup of hundreds of cargo vessels along one of the most important transport routes in the world. Or when international ports in China and South America have to curb their capacity due to the coronavirus or strikes. Or how storms in Sri Lanka and blocked ports in Australia have thrown global supply chains into disarray in the Asia-Pacific region. Not to mention pent-up demand for consumer goods in the US, which, combined with a multi-billion-dollar economic stimulus package, resulted in record import volumes and a shortage of truck capacity for onward distribution.
And if that weren’t enough, now the chip crisis is making headlines. The coronavirus is propelling digitalization, and semiconductor manufacturers are struggling to keep up. This is having huge repercussions: production in key industries such as automotive or mechanical engineering has stalled. Manufacturers are having to bank on their customers’ patience and, in some cases, pause production lines once more.
Upturn creates shortcomings
Bottlenecks and material shortages are plaguing industry in 2021. The causes are manifold. What’s crucial for stakeholders, however, is the knowledge that these bottlenecks are a sign not of crisis but of the eagerly awaited economic upturn. According to the economists at the Munich-based ifo Institute, there is nothing unusual about capacity and material bottlenecks at this point. When the economy was picking back up after the 2011 economic and financial crisis, there was a 19 percent material deficit. In the current coronavirus crisis, a deficit of 64 percent is hampering economic recovery—economists see this as a clear sign that the impact of the pandemic will be felt for a long time to come.
“Our employees put in a huge amount of effort and dedication to maintain a high level of reliability and performance throughout the pandemic, and this is now paying off. DACHSER is seen as a stabilizing factor in the market.” Burkhard Eling, DACHSER CEO
“Purchase prices, some of which have risen sharply, are another problem,” says Klaus Wohlrabe from the ifo Center for Macroeconomics and Surveys. “Currently, manufacturers are still meeting demand from their stocks of finished goods, but these are now also becoming noticeably depleted.”
All of this makes logistics companies more sought after as a partner and solutions provider than ever before. Economic recovery under the current conditions is not possible without them. A robust and balanced network is required; one that, as at DACHSER, remains effective and controllable even under the stress conditions caused by the pandemic and can thus demonstrate its “systemic relevance” every single day. DACHSER is prepared for the upturn: “We see economic catch-up effects directly reflected in the utilization of capacity within the DACHSER network. Our employees put in a huge amount of effort and dedication to maintain a high level of reliability and performance throughout the pandemic, and this is now paying off. DACHSER is seen as a stabilizing factor in the market,” says DACHSER CEO Burkhard Eling.
The sea container is a symbol of global supply chains. In terms of sea freight, the current lack of container capacity at European ports is painfully evident, with delays having become the norm. However, there is light at the end of the tunnel. “We’re yet to see how pandemic-related dispatch problems at sea, in the ports, or in the hinterland develop and how long it will take to clear the backlogs,” says Edoardo Podestà, COO Air & Sea Logistics at DACHSER, adding that shipping lines expect to be fully booked until at least the end of the year on almost all trade routes. “Following the disruptions experienced over the past few months, we’re seeing extremely high demand for consumer goods, boosted by the US economic relief package and the economic upswing also in Europe,” Podestà says. “Added to this is strong demand for furniture, as well as construction and renovation materials. The automotive industry is also getting back off the ground after the heavy setbacks it has suffered in the past two years—with huge demand for the transport of automotive parts.”
At the same time, high rates for sea freight are increasing the appeal of air freight. While air freight was around twelve times more expensive than sea freight before the crisis, the rate in May 2021 was “only” six times that of sea transport. In the first half of the year, DACHSER carried out more than 100 charter activities, regularly serving 12 different departure airports and 15 different receiving airports.
Considering the capacity shortages on container ships and the cargo hold of passenger aircraft (the latter is for transporting “belly freight”), Eling doesn’t expect any significant easing of the situation in the second half of 2021. This means freight rates will remain high, which will inevitably have to be reflected in the price development of goods and, in turn, logistics services.
Economic catch-up effects are directly reflected in the sheer volume of freight moving through the DACHSER network and the Road Logistics network in particular. “In the case of overland transport, the need for load capacity and for drivers has risen sharply,” says DACHSER COO Road Logistics Alexander Tonn. He adds that DACHSER has responded to bottlenecks by implementing various measures, for instance by focusing on the topic of planning transparency for transports and on creating a task force with the company’s own excellently trained professional truck drivers. But the overland transport situation in Europe still remains tense. “The idle time spent in transit terminals has, in some cases, risen considerably as a result of how the B2C proportion has grown. This reduces efficiency, makes for lengthier notification processes, and increases costs,” Tonn says. His concern is the current high price of wood, which is having a major impact on the price of pallets; packaging material providers are no longer in a position to provide the necessary number of pallets in the required quality.
For Eling, a robust and balanced network has a key role to play in this unique recovery situation. “All our customers are having to deal with a huge accumulation of products due to the pandemic. Either they are storing products until a more convenient time in the future, or they’re trying to bring them to market with special discount promotions. This means the quality factor will gain even more importance in helping logistics providers stand out from the competition,” Eling says. Through the flexible management of its own network organization, DACHSER helped its customers to further reduce their time to market and to develop new business models featuring the necessary tailored solutions.
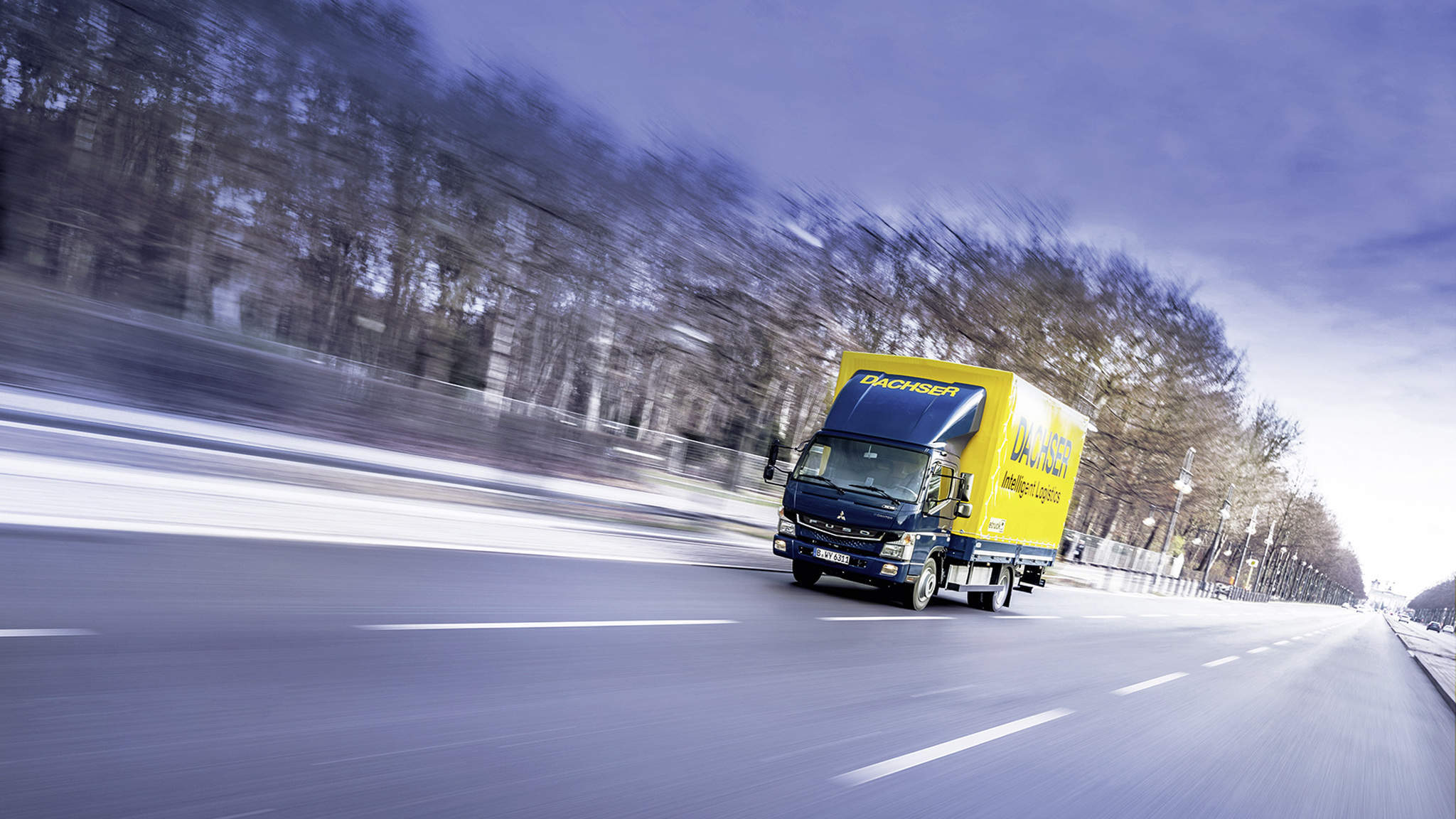
Sealing off the market is not a solution
When business models change, the question often arises as to whether the course of globalization should also be dialed back and the markets sealed off from external risks. Economists from the ifo Institute have spoken out against a general relocation of production back to Germany and against government intervention in supply chains. “A general return of supply chains would result in huge revenue losses,” warns Professor Lisandra Flach, Director of the ifo Center for International Economics. Instead, the sources of supply for the economy ought to become more internationally diverse. Free trade agreements could reduce trade costs and decrease dependencies on individual nations. This calls for a deeper European Single Market and a stronger World Trade Organization.
“We’re also noticing that a lot of our customers are turning their attention to the future configuration of their supply chains,” Eling says. “Many of them are specifically looking at the security and resilience of their supply chains and are exploring more flexible transport options.” At the same time, Eling is confident that global supply chains will continue to exist. “Our customers aren’t looking to completely overhaul their supply chains, let alone turn their backs on globalization.” He adds that complete nationalization would also be “suboptimal and risky,” instead suggesting that an “intelligent mix of regional and global production structures” is a better way of preparing for future crises. Warehousing is also being expanded regionally to better safeguard against disruptions to the supply chain.
According to Eling, this explains why flexibly structured logistics networks will be more sought after than ever before; networks that are able to combine different carriers in the best way possible with the customer’s needs in mind. Throughout the pandemic, he says, DACHSER has shown that the logistics provider and also the people that fill the network with life are ideally positioned for the supply chains of the future.
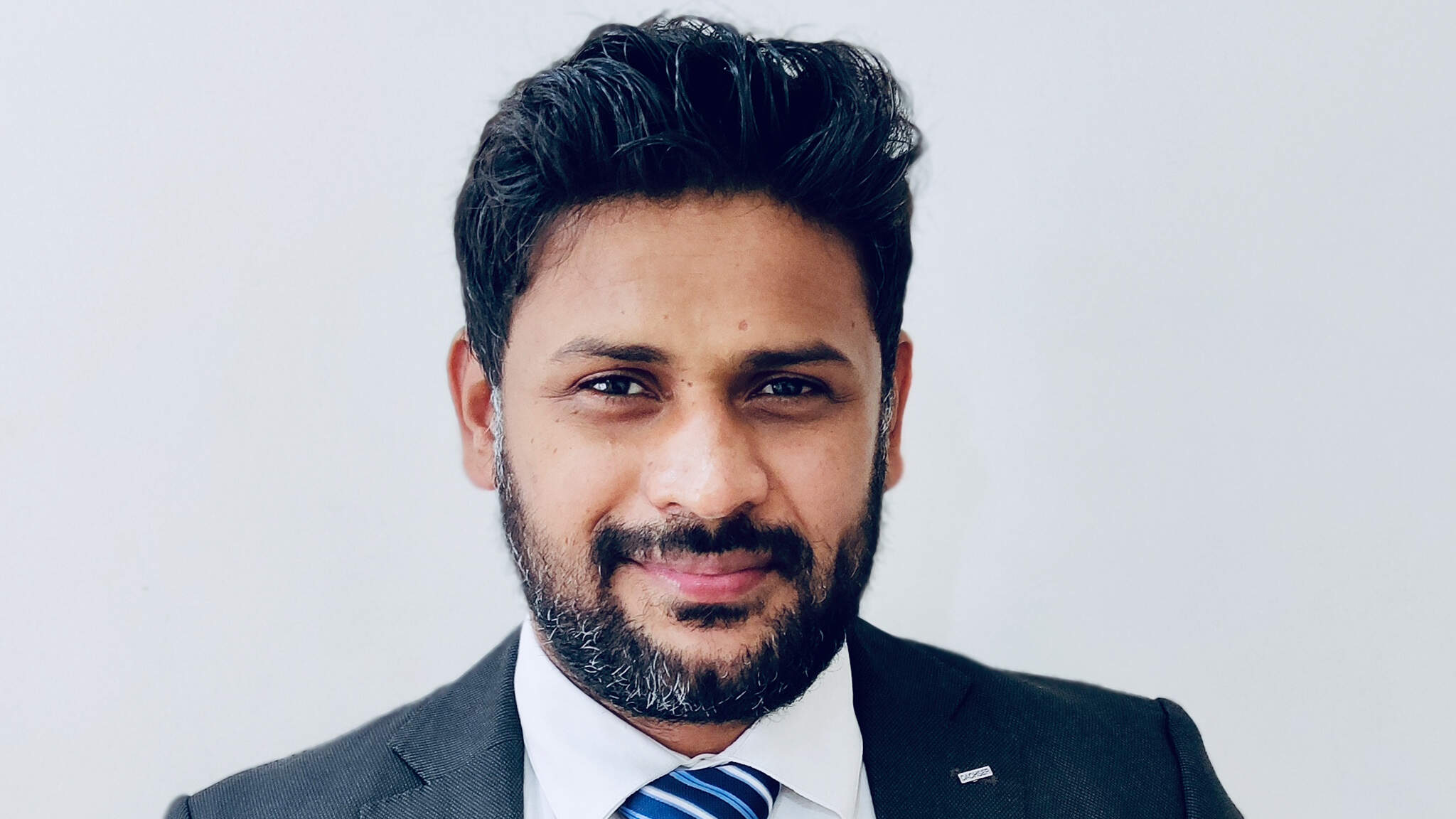