Ahead of the curve – customer case Aptiv
Radical upheavals are in store for the automotive industry. Aptiv is a leading technology company innovating at the intersection of disruptive trends in the mobility industries. And intelligent logistics is making a crucial difference.
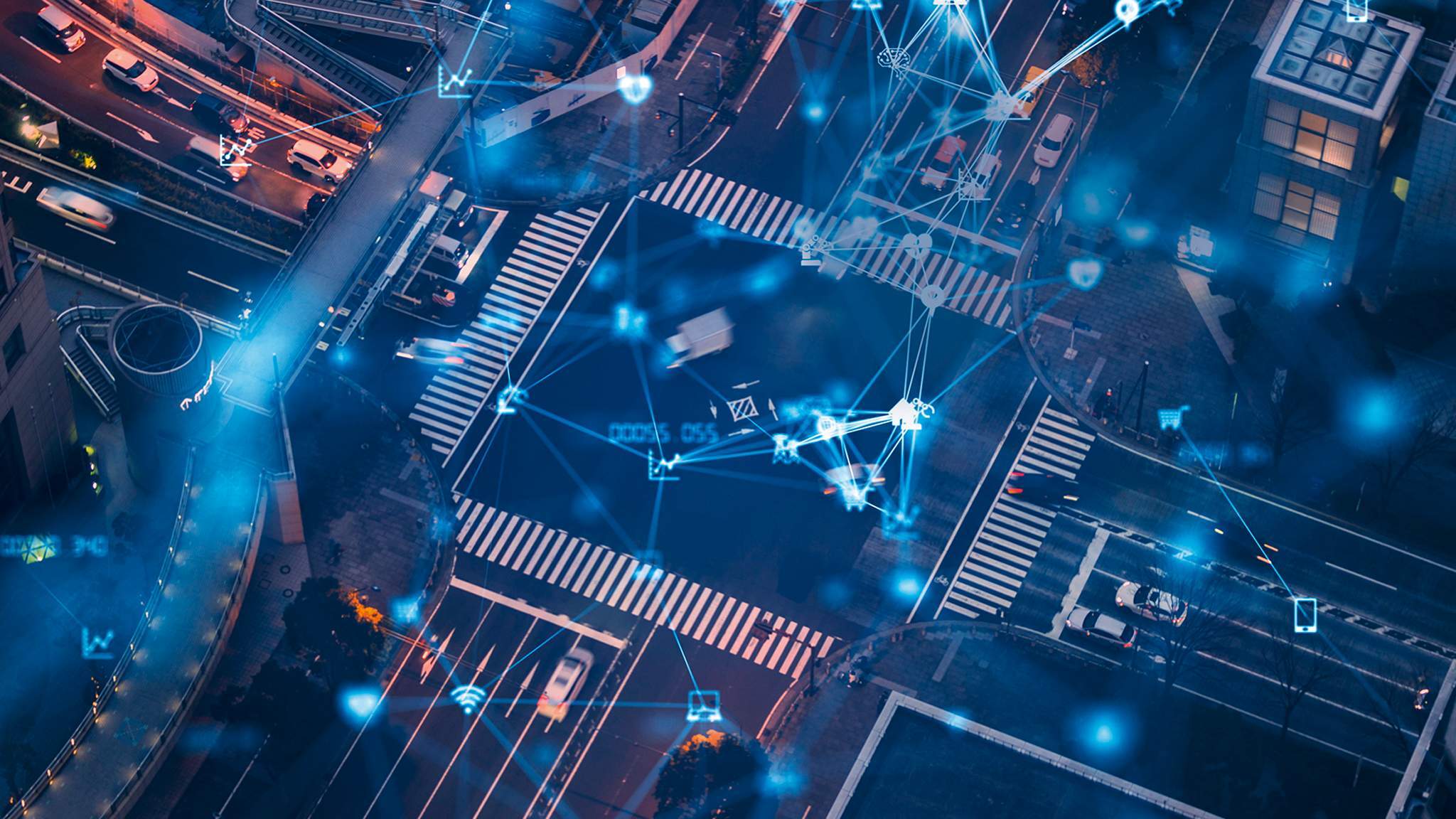
Over six years ago, Aptiv made the impossible possible. A dedicated team and technology helped complete the longest automated vehicle drive ever—traveling nearly 3,400 miles from San Francisco to New York City, with 99 percent of the drive in fully automated mode. The vehicle successfully navigated complex driving situations, collecting data essential to advancing the emerging active safety technology sector.
Aptiv’s unique position as the only provider of the brain (software and compute) and nervous system (power and data distribution) for mobility solutions is allowing the company to conceive, specify, and deliver the advanced vehicle architectures of the future. Aptiv’s mission is clear: “We use our portfolio of technologies to make vehicles safer, greener, and more connected and enable the future of mobility.”
To gear up for present and future tasks, the company is collaborating with over 100 suppliers, including many from Germany. DACHSER supports Aptiv in Asia Pacific, where it has numerous manufacturing facilities that produce parts and systems for local as well as global markets.
Aptiv’s demands on its suppliers and logistics are correspondingly high. Even a single missing part could mean not being able to deliver a complex unit such as the one that controls the energy flow when recharging an electric car. Consequently, the company was looking for a logistics partner that offers everything from a single platform. And DACHSER had just the right answer: its DACHSER Automotive Logistics industry solution.
“Like clockwork”
DACHSER now collects the products from Aptiv’s European suppliers and consolidates the consignments for onward transport worldwide, generally by sea freight. “Our European transport network is tightly interconnected and very flexible, and it offers the highest quality standards and short transit times. This lets us handle orders for our automotive customers efficiently, seeing them through to destinations all over the world—and it ensures complete transparency at every stage of the transport chain,” says Stefan Dahnken, Department Head DACHSER Automotive Logistics. He adds that to manage the automotive sector’s complex supply chains, DACHSER can apply not only its expert know-how but also the tried-and-tested combination of its strong European Logistics and Air & Sea Logistics networks with precisely timetabled transit times. “The individual elements of our automotive supply chain run like clockwork to keep transit times consistent and reliable,” he says, explaining the recipe for success. DACHSER has set up an Automotive Coordination Tower in Hamburg to provide a corresponding service and control unit for the sector. Its staff of 40 ensures optimal workflows in planning and booking, in the control and organization of pre-carriage, in customs clearance, and in the selection of suitable means of transport.
"The individual elements of our automotive supply chain run like clockwork to keep transit times consistent", says Stefan Dahnken, Department Head DACHSER Automotive Logistics."
For Aptiv, DACHSER’s Neuss branch in North Rhine-Westphalia is an important hub in the DACHSER network. It is where the trucks arrive carrying supplier products from various European countries ready for consolidation and onward transport. Shipping containers are then loaded just a few kilometers further down the Rhine at the inland port of Duisburg. Here, the employees are careful to make best possible use of the cargo space. With widely varying product shapes—including everything from cable spools to palleted goods to individual boxes—this is not always easy. Furthermore, stackability is sometimes greatly restricted for boxes containing sensitive electronic components. This makes it all the more important to bring the consolidated shipments to their destination with as little transshipment as possible. Not to mention that having many individual shipments means a lot of customs red tape and occasionally longer transit times.
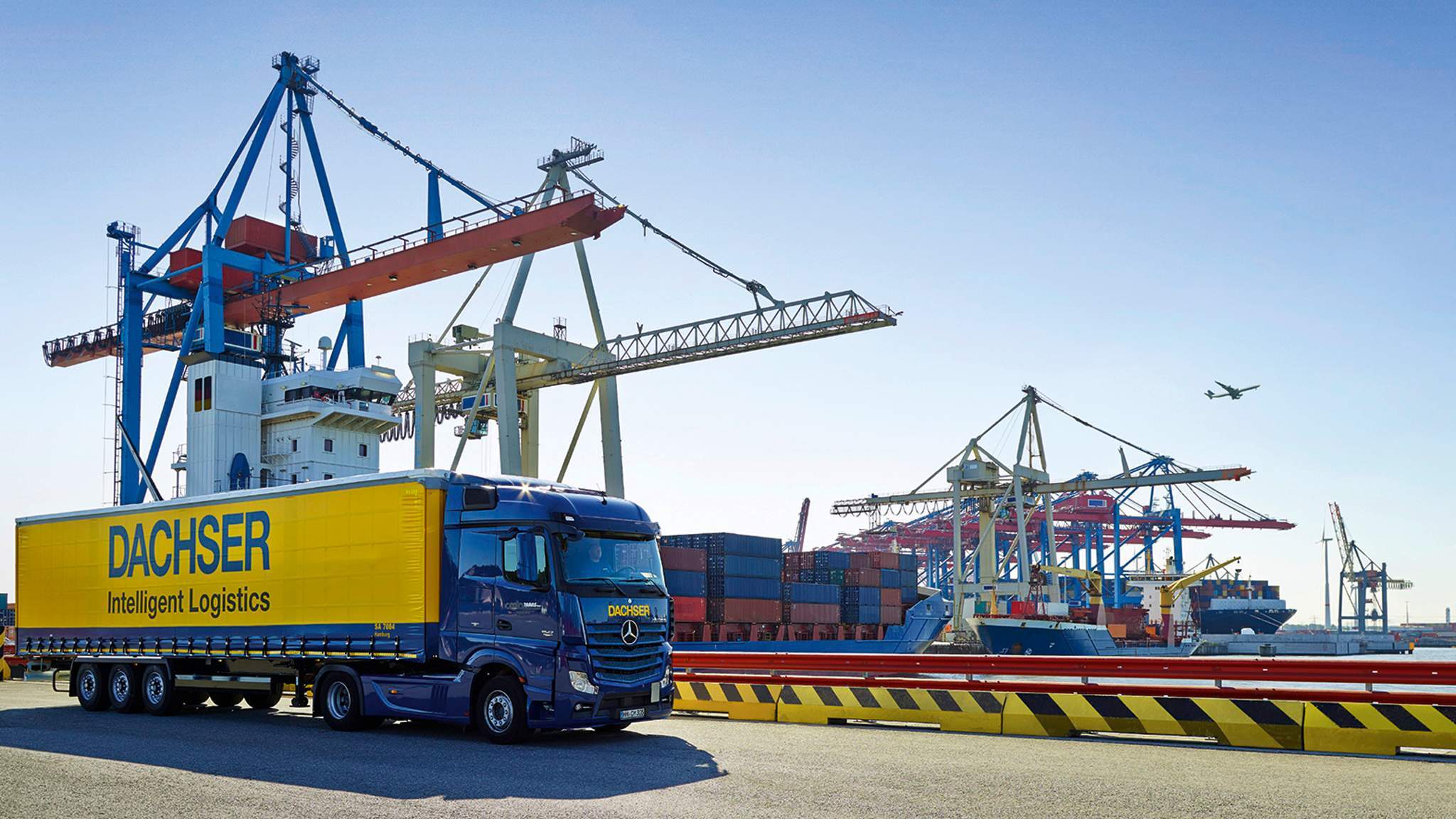
All from a single source
DACHSER has since managed to increase the average utilization of container capacity by 20 percent for Aptiv. In addition, the customer benefits from continuous shipment tracing by means of Serial Shipping Container Codes (SSCCs). “Continuous improvement of cost and efficiency in complex supply chains were a key target for Aptiv,” emphasizes Martin Ma, Department Head Key Account Management Air & Sea Logistics Far East at DACHSER. Ma is Aptiv’s direct contact and looks after the customer from his office in Shanghai.
The DACHSER Automotive Logistics corporate solution grows with its customers as a scalable solution. If the customer adds new suppliers or production sites, both the pickup matrix and the delivery runs are adapted accordingly. And in situations where speed is of the essence, shipments take the “fast lane” with the corresponding targospeed product—in overland carriage with subsequent intercontinental onward transport by airplane or rail—when a sea route would take too long. On this point, DACHSER is just as flexible as Aptiv. After all, a new battery technology or new recharging standard for electric cars can establish itself overnight. And if it does, the supply chain has to remain reliable, plannable, and flexible.
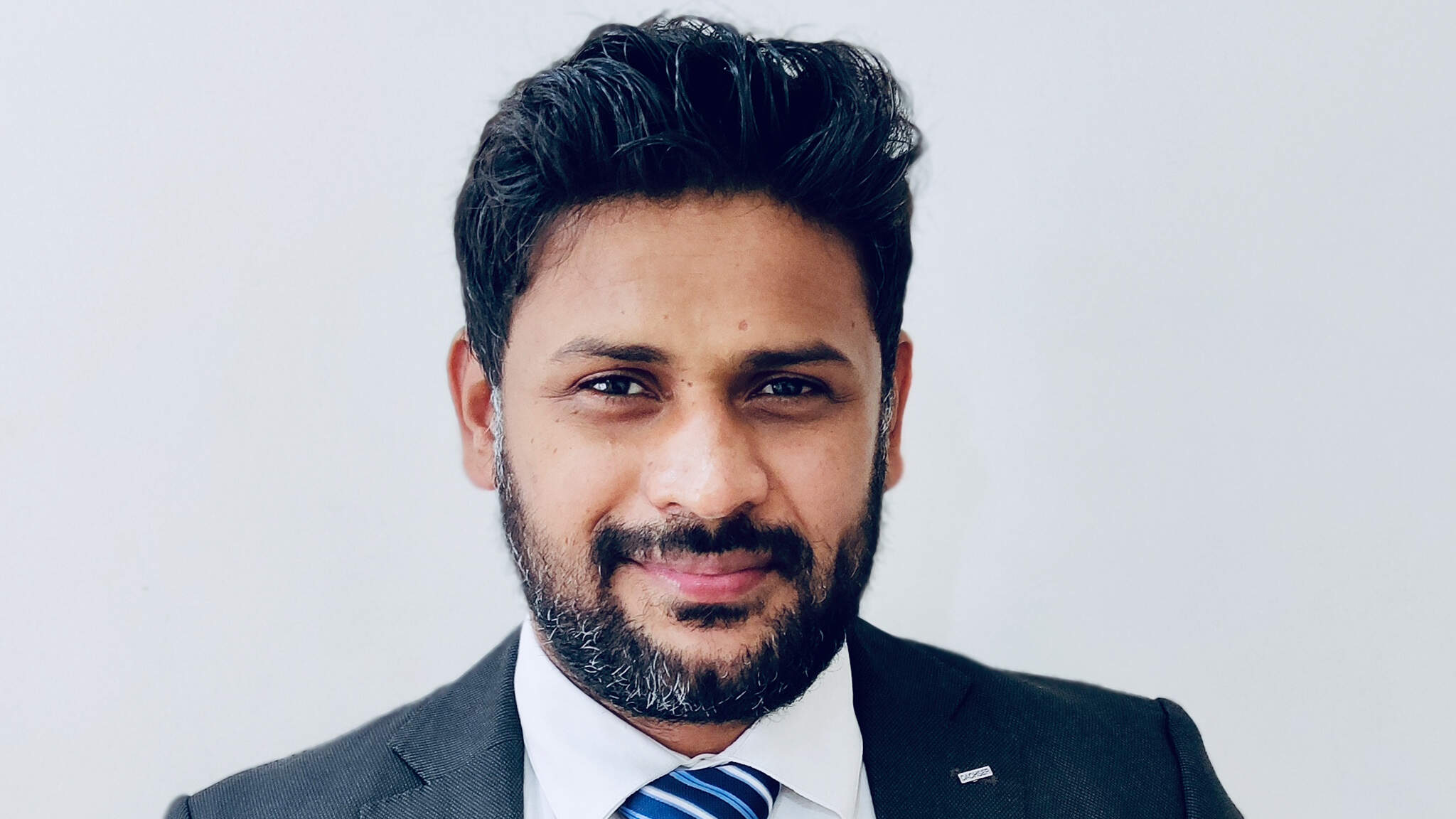